Optimization of Supply Chains in the Automotive Industry with our Customer RIO
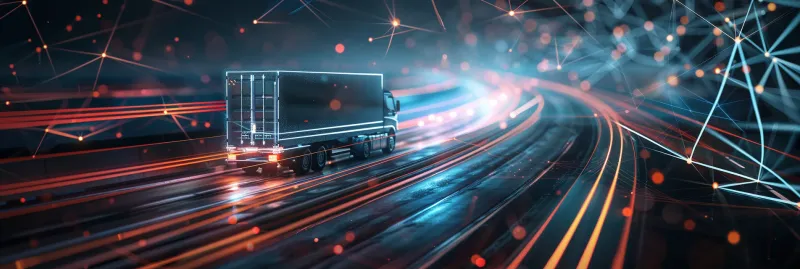
Which parts does a supplier need for an automotive manufacturer, when, and in what quantity? Which logistics service provider is responsible for the transport of the goods? Our customer RIO answers these questions with its new software solution for supply chain optimization in the automotive industry.
From 2 to 1: Efficient Shipping Proposals and Error Avoidance
The starting point involved two separate cloud applications, namely
a platform on which manufacturers can post their material requirements, and suppliers can see and configure material deliveries, and
a free portal on which, in particular, small and medium-sized transport service providers can easily receive and confirm transport orders.
Our TNG colleagues, together with RIO employees, have expanded these two systems and linked them more closely. In the past, suppliers had to monitor the required demand and transport capacities independently, as well as determine and commission the responsible transport service provider. The new system automatically combines all deliveries for a recipient in shipping proposals for the next 14 days. Based on a proposal, a transport can be commissioned from the responsible service provider with one click, and no further communication outside the application is necessary. This reduces the potential for incorrect bookings and the required time expenditure on the part of the supplier.
The new system also offers advantages for automotive manufacturers, as the association of exchanged EDI messages to a transport is simplified using only one system. The application thus increases transparency in the supply chain and the efficiency of the entire transport network.
Modern Techniques: Trunk-Based Development and Continuous Deployment
The development was carried out using modern techniques. The use of Trunk-Based Development secured with Feature Toggles, offers the following advantages, among others:
Deployments can be carried out directly in production - often more than 15 per day.
Certain functions can be made selectively available to individual or all users.
Existing customers of both RIO applications do not notice any downtimes despite continuous modifications.
Success through Close Cooperation and Continuous Improvement
Close cooperation between RIO's internal developers and service providers such as TNG contributed significantly to the project's success. Thanks to DevOps techniques, responsible teams can directly identify and resolve smaller problems. Additionally, they collect feedback through user surveys and independently implement it.
Positive Feedback and Ambitious Goals
The results of this approach are already being rated very positively by users - employees of suppliers to an automotive group. Among other things, the clarity of the user interface and the fact that the application is self-explanatory are highlighted. The automatic selection of the responsible transport service provider and the very simple commissioning of the transport are also well received.
We are very pleased about the positive feedback and are now working together on the next step of using the new solution to handle all European suppliers and the associated material transports of all involved brands.